Business consultants
Construction Failure Analysis Consultants: 21
Global Infrastructure Construction Consultant Thomas Young
Thomas J. Young, PE
Founder, Chairman, CEO
Roseville CA
95747
USA
phone: 916-662-5022
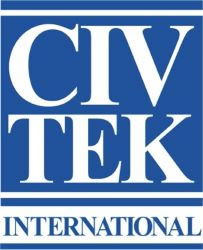
Roofing Waterproofing Consultant Timothy Barrett
Timothy M. Barrett, RRC, CSI, CDT, GRP
President
33 Stonehouse Rd.
PO Box 412
Millington NJ
07946
USA
phone: 908-647-0238
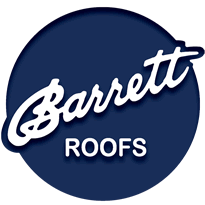
Architectural Review Consultants
Dan Weekes, AIA, NCARB, BECxP, CxA+BE
Jim Stutzman, AIA, NCARB, CSI
8500 East 116th Street, #6142
Fishers IN
46038
USA
phone: 317-746-8292
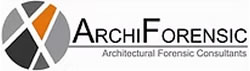
Power Production Design Consultant Ole Haaland
Ole Haaland, PE
626 Admiral Drive
C-537
Annapolis MD
21401
USA
phone: 410-268-6321
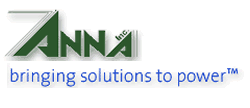
Pavement Failure Consultant Wayne Seiler
Wayne Seiler, PhD, PE
205 Ramblewood Drive
Chatham IL
62629
USA
phone: 850-647-2740
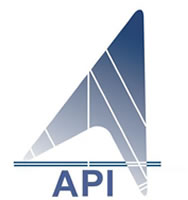
Technology Analysis Consultant William Acorn
William Acorn, P.E., CFLC, FASHRAE
Principal
16420 N 92nd St
Suite 224
Scottsdale AZ
85260
USA
phone: (602) 888-7250
fax: 602-888-7250
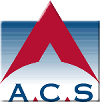
Featured resources
by Lorne G. Everett, PhD, et al
by Dave Gerr, CEng, FRINA
by Donald C. Austin, MD