Farming is a dangerous occupation. Tractor rollover accidents have been killing people since the 1920's. In 1990, the National Safety Council estimated 460 people were killed while operating tractors. Tractor rollover caused 239 of these fatalities. Another estimate suggests a more conservative number of annual fatalities - 132, that are the result of tractor rollover accidents. In a four-year period in Pennsylvania alone, 72 people died as a result of tractor rollover accidents. The director of the National Institute for Occupational Safety and Health (NIOSH) said it best when he called tractor rollover accidents an "occupational obscenity". NIOSH holds that nearly all rollover-related fatalities could be prevented.
Why do tractors rollover?
Tractor instability is the underlying factor of rollover accidents. The center of gravity is an important concept in understanding tractor instability. The tractor's center of gravity can be thought of as the balance point of the tractor. The lower the center of gravity, the more stable a vehicle is, the higher the center of gravity, the less stable a vehicle is, and the more likely it is to rollover. Tractors have a high center of gravity to allow cultivating tall row crops like corn. The enormous size of the rear wheels contribute to this elevated center of gravity. We all know that SUV's have a higher chance of rolling over than a car. This is the same idea - SUV's have a much higher center of gravity than an automobile.
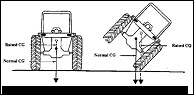
Figure 1: A raised center of gravity decreases stability
A Bad Situation Gets Worse
A tractor has a high center of gravity to begin with. There are many things which can cause the center of gravity to be raised, making the tractor much more unstable. Many farmers equip their tractors with after-market front-end loaders. Tractors are used for many different tasks, and using the tractor with the loader full is a basic requirement of a tractor. A tractor with questionable stability suddenly gets much more unstable when a loader is attached. Safety Engineering Resources found that adding a raised, fully loaded bucket can raise the center of gravity of the tractor more than 26 inches. Adding a high-mounted liquid fertilizer tank can raise the center of gravity also.
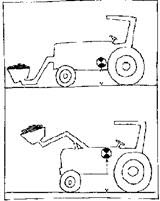
Figure 2: Lifting a loader raises the tractor's center of gravity.
To determine the effects of this raised center of gravity, Safety Engineering Resources determined the rollover angle, the angle where the tractor is balanced. This is a useful measure of tractor stability, since tractors are driven across slopes, on road embankments, and other places where the tractor will be traveling at an angle. We found that the tractor we were testing would tip over if it reached an angle greater than 39 degrees. This angle is twenty degrees less than it was when the tractor did not have the loader attached.
Although tractor operators are sure to be aware of rollover accidents, what they don't know is how easily they can occur. A front-end loader also puts more weight towards the front of the tractor, which can make the tractor more difficult to turn, which can lead to an accident.
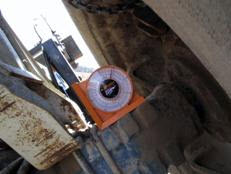
Figure 3: Safety Engineering performing tractor stability tests
The following graph shows the change in rollover angle. The rollover angle is a measure of the stability of the tractor which incorporates the weight distribution, the center of gravity, the effect of adding a loader and a load.
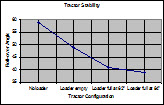
Figure 4: Chart showing decreasing stability due to raising tractor loader.
Centrifugal force is another factor which can cause rollover accidents. This is the force created from driving the tractor in an arc of some sort. Centrifugal force is dangerous and unpredictable - the force it exerts on a tractor multiplies quickly as the tractor's speed is increased. Doubling the speed of a tractor increases the chance of an overturn by about four times. As the centrifugal force increases, quick turns can rapidly change the vehicle's center of gravity and cause an overturn.
There are many events that can trigger a rollover accident to a tractor with a high center of gravity. Rocks, stumps, and holes in fields can exert upward force on the tractor if driven over. This upward force can cause the tractor to roll. Drivers raising their loaders while driving to dump their load can easily lose stability of their tractor, due to the elevated center of gravity, resulting in a rollover.
Tractor operators sometimes think that they can prevent a rollover accident by turning their tractor towards the direction of instability. Although it's worth a try, people cannot react before an accident occurs. Side over-turns can occur in 0.75 seconds. Most people need between .3 and 1 second or more to react to an event, once realization has been made.
The solution - Rollover Protective Structures (ROPS)
Tractors are unstable. Attachments make them more unstable. Safe operating practices can reduce the chance of a rollover accident, but not eliminate it. Tractor manufacturers have a responsibility to protect the users of their products from harm. The fact that rollover accidents occur all of the time during normal tractor use signifies that the accidents are not due to some unforeseen use. Tractor manufacturers have not solved the root problem, tractor instability. Ideally, tractor manufacturers would take the ball and come up with a tractor design that is not inherently unstable. They have yet to do this. The only other option to tractor manufacturers while they continue to sell dangerous products, is to guard the tractor user from harm. The National Safety Council's Hierarchy of Design holds that if the hazard cannot (or will not) be designed out of the product, then the user must be guarded from the hazard. This is the function of Rollover Protective Structures (ROPS). ROPS are high-strength steel cages that enclose the operator zone and protect the driver in the event of a roll over. ROPS are designed to limit roll to 90 degrees. Seat belts are a very important integral part of the ROPS system. Tractor users have been severely injured or killed when they rolled their tractors, equipped with ROPS, without safety belts in use. They were crushed by the tractor when they fell out of the operator's seat when the tractor rolled over. In the event of a roll over, the driver can easily be dislodged from the driver's seat by gravity or by the centrifugal forces generated in a roll over accident. A seat belt keeps the operator in the driver's seat and allows the ROPS to perform its protective capabilities. Without a ROPS, a seat belt can increase the chances of injury in a roll over accident. A driver who is held in his or her seat in a roll over will be crushed if the tractor rolls 180 degrees or more.
Tractor owners without a ROPS should equip their tractors with a ROPS. There are many after-market options today. To assure that the ROPS has been designed and tested properly, the ROPS should meet or exceed the performance standards established by the American Society of Agricultural Engineers (ASAE), the Society of Automotive Engineers (SAE), or the Occupational Safety and Health Administration (OSHA).
History of ROPS Standards
Tractor rollover accidents are not new, and neither are ROPS. Tractor rollover fatalities were first reported in the 1920's. The first rollover protection structures appeared in the 1950's. Many studies were done in the 1950's concerning tractor roll over accidents and ROPS.
In 1959, the Army Corps of Engineers, the U.S. Department of the Interior, and the states of California, Oregon, and Washington all began requiring ROPS on their tractors. Illinois and North Dakota both passed laws requiring all tractors purchased after 1960 to have rollover protection. In 1965, ASAE and SAE formed a safety committee to research ROPS and produce a standard. This committee reviewed many tractor rollover studies, domestic and foreign. This led to the ASAE S306 Standard in 1967, "Protective Frame - Test Procedures and Performance Requirements." Also in 1967, The National Safety Council published an article recommending that all tractor manufacturers install rollover protective systems. In 1971 California required all tractors with more than twenty horsepower, manufactured after April 1, 1971, to be equipped with ROPS. On October 25, 1976, the Occupational Safety and Health Administration (OSHA) issued regulations requiring all tractors used by an employee manufactured after October 25, 1976 to be equipped with ROPS. In 1977, California passed legislation requiring all tractors older than 1971 to be retrofitted with a ROPS by 1977.
Effectiveness of ROPS
Do ROPS Work?
Numerous studies have shown that ROPS, along with seatbelt use, drastically reduces tractor rollover fatalities. When North Dakota implemented overturn protection on its highway mowing machinery, nearly ALL of the state's tractor fatalities were eliminated. Illinois also required ROPS on all mowing tractors purchased after 1960. This greatly reduced the state's tractor fatality rate. A study by the National Institute for Occupational Safety and Health (NIOSH) in Nebraska found that since 1967, there were 250 tractor rollover accidents on tractors without ROPS, and 61 tractor roll over accidents on tractors with ROPS. Forty percent (100 people) of the drivers on tractors not equipped with ROPS died in the accidents. Only two percent (one person) of the accidents involving tractors with ROPS occurred in a fatality, and that person was not using a seat belt. Another study by the University of Iowa and the Iowa State University found that tractor operators survive 95% of the time in roll over accidents on tractors equipped with ROPS. This same study found that tractor operators survive only 25% of the time in roll over accidents on tractors without ROPS. A paper put out by the University of Illinois Agricultural Engineering Sciences Department states that farmers whose tractors are not equipped with ROPS are exposing themselves to "unnecessary risk". These studies show the effectiveness of ROPS. Since ROPS have been proven to save many lives, why aren't they required on all tractors, past and present?
Conclusion
Today, there are many product liability cases involving ROPS. Some states have made this difficult by making restrictive laws that prevent tractors to be shown as defective without a ROPS, since tractor operators should know that tractors can roll over. They are in essence putting the blame on the operator not the manufacturer. We are currently involved in a ROPS case where we have to show that tractor operators don't realize how easy it is to roll a tractor. Cases like this may help to change the laws and require the tractor manufacturers to do what they should have done in 1976 - retrofit their tractors with ROPS. The reams of accidents and fatalities proves, in my opinion, that a tractor without a ROPS is unreasonably dangerous.