Safety Engineering Resources has had the opportunity to learn a great deal about using fiberglass in structural applications, which are simply applications that must support some sort of load. Using fiberglass as a structural material was brought about by the advances made by organic chemists in recent decades in the field of plastics. Using fiberglass as a structural material has "necessitated the development of analytical and design procedures which have not been generally required in treatments involving the more standard structural media." ( GRP in Structural Engineering, M. Holmes & D.J. Just, p. v). Many universities' engineering programs do not touch on designing structural components with fiberglass. Many of the concepts are the same as more traditional materials, although fiberglass has specific strengths and weaknesses that must be considered in any glass-reinforced plastic design. Glass-reinforced plastics are now used in a variety of products including heating ducts, pipes, ladders, liquid vessels, showers, baths, boats, hand tools, automobile body parts, seating products, swimming pools, swimming pool accessories, church steeples, roofs, and chimneys. Since fiberglass can be formed into any shape, the possibilities of uses are endless.
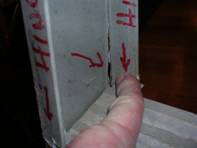
Figure 1: Fractures in fiberglass
Fiberglass Background
Plastics alone are not suitable for structural applications due to low stiffness and ultimate strength. Plastic in this aspect is analogous to concrete. Concrete alone is unsuitable for applications in which tensile stress is produced and must be reinforced to produce a material with reasonable structural strength. Polyester resin is the most common type of plastic used in structural engineering applications. Plastics also must be reinforced to produce a material that can be used in structural applications. Glass fiber is often used to reinforce plastics due to its high strength and stiffness characteristics and its ability to bond easily with the polyester resin. The strength and stiffness characteristics of GRP's is largely dependent upon the strength of the reinforcing material itself. Carbon or boron fibers can be used to reinforce plastics that have superior structural properties, but this is rarely done due to high production costs. Polyester resin can be reinforced with chopped strand mat, rovings and woven rovings, and woven fabrics. Chopped strand mat is made from glass strands that result in a random mixture of filaments and portions of strands. The strand-filament is bonded to resin binder which forms a fiber mat whose strength is determined by the number of glass fibers present. This type of reinforcement is the most widely used, but is not suitable in designs where high strength is a requirement. Rovings are groups of continuous parallel glass strands, bundled together. This type of reinforcement exhibits high strength in the direction of the strands only. Woven fabrics are used only when extremely high strength GRP's are needed. The strands in woven fabrics are twisted producing a higher density of reinforcing glass strands.
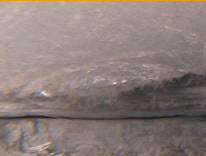
Figure 2: Microscopic view of fiberglass fracture
Design and Fiberglass
What is alarming is that engineers are not being taught how to design with fiberglass. Most universities have a very limited amount of actual design education curriculum in their engineering programs. The design courses that engineering students do get normally cover design aspects of only steel and aluminum. Rarely are any composite materials covered in design courses. Composite materials such as plastics and glass-reinforced plastics have very unique material properties that must be considered in the design process.
The design process of composite materials is unique. The composite material and the product are usually manufactured at the same time. Molds must be created in the shape of the components that are costly and expensive to produce. This means that there can be little to no change in the design after the initial manufacturing, unlike manufacturing products with more conventional materials. This can be a big problem if some weakness is identified in the design. Another factor in fiberglass design is that the strength of glass-reinforced plastics is highly dependent upon the strength of the individual glass fibers. A problem is that fiberglass has strength and rigidity only when it is loaded in a direction parallel to the fibers in the material. When it is loaded in a different direction, fiberglass is much weaker. Another big problem with designing fiberglass structures is that property data for an exact polymer can be difficult to find.
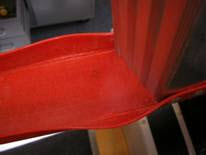
Figure 3: Fiberglass failure
Only recently have codes of practice been developed for some aspects of fiberglass design. Without a standardized design procedure, research and experience must be utilized to produce an effective fiberglass structure.
Long-Term Use Problems
Structural products made out of fiberglass experience a loss of strength with time, with use. Studies have shown that with exposure to a normal air environment, fiberglass that is loaded can lose over 60% of its strength after only 417 days of continuous use. This is another way that fiberglass differs from traditional construction materials, and must be accounted for in any structural design.
Effect of Temperature on Strength
The strength of reinforced plastics is reduced when exposed to elevated temperatures. The exact amount of strength reduction will vary between different glass-reinforced plastic composites. Changes in the Modulus of Elasticity correspondingly drop with increases in temperatures. Strength and stiffness are reduced nearly 50% at 200 degrees F.
Design Factor of Safety for Reinforced Plastics
Many products and materials have allowable working stresses that are specified by Codes, Standards, or recognized authorities. Allowable working stress is the amount of stress that a design can withstand over an extended period of time. Allowable working stress takes into account factors that can affect the strength of a design including environmental effects, average loading, and maximum loading. Besides all of the known factors that affect the stress in a design, a design factor of safety must be included to ensure a design that will not fail. A product cannot be designed to incur stress right up to the maximum allowable stress. Despite the most vigorous design procedures that try and account for any and all variables, there must be a margin of safety left in any design. The design factor of safety for conventional materials such as steel has been backed up with decades of experience. Reinforced plastics is a relatively new material, and there is not this benefit of extensive experience. A minimum factor of safety of 4.0 is recommended for any fiberglass structure. For situations involving fatigue, repeated loadings, a factor of safety of 6 is required. Impact loads calls for a factor of safety of 10.
Finite Element Analysis
To be able to give a design an adequate factor of safety requires knowledge of the stresses that will be created by normal loading of the product. Finite element analysis (FEA) is a computer program that can accurately determine the stresses at any point in a model. This is particularly useful for geometrically complicated designs. The following is an example of FEA output.
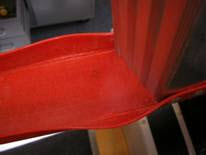
Figure 4: Example of FEA output
What's This Mean to Me?
What does all of this mean to you, an attorney who deals with potential product liability cases? The lack of education about designing with polymers, the unconventional structural characteristics of fiberglass, the loss of strength and rigidity to environmental effects, and inadequate design factors of safety all increase the likelihood of failures of products manufactured out of fiberglass.