According to the OSHA regulations, a confined space is anyplace that meets the following criteria:
(1) Is large enough and so configured that an employee can bodily enter and perform assigned work; and
(2) Has limited or restricted means for entry or exit; and
(3) Is not designed for continuous employee occupancy.
Obviously, tanks and other large vessels fall into this category, but so do pits or excavation areas. A permit-required confined space is a confined space with one of the following:
(1) Contains or has a potential to contain a hazardous atmosphere;
(2) Contains a material that has the potential for engulfing an entrant;
(3) Has an internal configuration such that an entrant could be trapped or asphyxiated by inwardly converging walls or by a floor
which slopes downward and tapers to a smaller cross-section; or
(4) Contains any other recognized serious safety or health hazard.
These spaces require specific procedures when they must be entered for maintenance or other reasons. The procedures need to cover all aspects of hazard removal and prevention. Because so many different types of confined spaces exist, a blog can't cover all the aspects the entry procedures should consider.
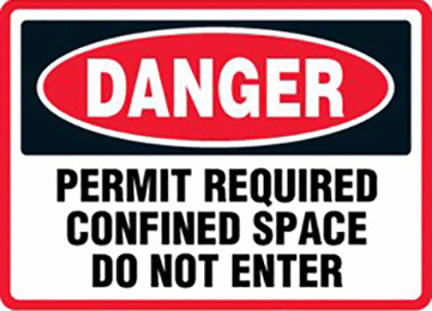
Figure 1: A typical warning found on a confined space.
Instead this blog will consider just one area and review a case where it was improperly performed. Let's look at isolation. Unless you are dealing with a pit or excavation, the confined space to be entered must be isolated from the process of which it is a part. OSHA defines isolation as "the process by which a permit space is removed from service and completely protected against the release of energy and material into the space by such means as: blanking or blinding; misaligning or removing sections of lines, pipes, or ducts; a double block and bleed system; lockout or tagout of all sources of energy; or blocking or disconnecting all mechanical linkages."
Warren investigated a case where a worker was doing maintenance on the trays of a stripping column (a vertical tube 6.5ft wide and 78ft tall). While he was inside, approximately 100 gallons of process fluid entered the column from a condenser. He succumbed to the vapors and died inside the vessel. The mistake made in this instance was isolating the stripping column 'system' from the rest of the plant instead of isolating the column itself from all surrounding equipment.
In conclusion, permit-required confined space entry is similar to sky diving. There are definite risks involved, but they can be successfully mitigated; and are more often than not. However, when they are not, things can go very bad, very quickly! So take the time and prepare your confined space entry procedures with a safe exit in mind. The specific OSHA regulation that covers this topic is 1910.146 and spells out exactly what is required.
Jennifer Morningstar, BSChE, PE, CFEI has 19 years of industrial experience. Her areas of emphasis include chemical release & exposure, OSHA process safety management, industrial accident investigation, fires & explosions, and scope of damage/cost to repair analyses. She is an OSHA-trained Process Hazard Analysis study leader and completed Root Cause Failure Analysis training to become an Incident Investigator. She has experience as an energy management consultant in a variety of industries including mineral extraction, pulp & paper, animal harvesting & packaging (including rendering) and grain milling. Jennifer holds a Bachelor of Science Degree in Chemical Engineering from Virginia Polytechnic Institute and State University as well as a Masters of Business Administration from the University of South Carolina.
©Copyright - All Rights Reserved
DO NOT REPRODUCE WITHOUT WRITTEN PERMISSION BY AUTHOR.