The Occupational Safety and Health Administration (OSHA) estimates that approximately 95,000 injuries occur each year due to forklifts. The estimated number of forklifts being used in the United States is determined to be about 800,000. This means that about 12% of the people using forklifts are being injured each year. This is a staggering statistic. 100 people are killed each year in a forklift accident.
Types of Forklifts
Motorized Pallet Trucks
Motorized pallet trucks are small lifts that have powered drive systems. There are two types of motorized pallet trucks - "walkies" and "riders".
"Walkie" motorized pallet trucks are an economical alternative to rider pallet trucks or forklifts. They are operated by a control arm, which the operator holds while he or she walks alongside or behind the lift. The maximum speed of walkies is low, since the operator must keep up with the lift.
Rider pallet trucks are powered pallet lifts that have a small platform or stance for the operator to ride on. Rider pallet trucks are fast, which is why they are used often in large warehouse and manufacturing applications. Rider motorized pallet trucks have few controls, making operator training an easy task. High lift pallet trucks are designed to raise and lower objects to elevated heights. Front rider pallet trucks have the operator stance located between the front of the lift and the battery storage, in the middle of the lift.
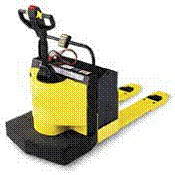
Rider Pallet Truck
"Walkie/Rider" pallet trucks are essentially a combination of a walk-behind pallet truck and a rider pallet truck. The operator stance on walkie/riders is very small to allow the operator to get off of the pallet truck and control the lift from a walking position.
Sit-down counterbalanced lift
Sit-down, rider controlled forklifts are arguably the most widespread of industrial lift trucks. The basic design consists of a fork and mast like pallet trucks, an operator compartment situated on top of and in front of the engine and battery of the forklift.
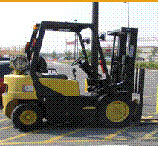
Sit Rider Forklift
Other lifts
Order picker trucks are essentially lift trucks that are controlled from a carriage where the operator stance is located. Straddle trucks carry long material like pipes, boards, and trees. Another type of straddle truck is designed to handle pallets and has outriggers. Rough terrain forklifts are forklifts that are designed to be used outdoors, on dirt, rock, grass, mud, snow, etc. The automated guided vehicle (AGV) represents the future of materials handling technology. AGV's do not require operators, but travel along a route that is demarcated by frequency sensors, light beams, or induction tape.
Forklift Accidents
Pedestrian Collisions
Pedestrian collisions occur frequently on forklifts. A common accident occurs when a pedestrian walkway crosses a vehicle pathway and is not seen by the operator due to the field of view being blocked by part of the lift. Other blind spots can cause collisions when either a pedestrian or a lift operator does not have time to react to the presence of the other.
Collisions with Stationary Objects
A collision with stationary objects is also a concern for lift manufacturers. Collisions with stationary objects are easier to control than collisions with moving objects like personnel. Common collisions with stationary objects include collisions with shelving, walls or other permanent fixtures.
Walkie and Rider Pallet Truck Accidents
Accidents with motorized pallet stackers such as "walkie" stackers, rider stackers, or the combination walkie-rider often involve a collision between a stationary object and part of the operator's body. The operator stances found on these lifts are often too small - operators often have a large portion of their bodies outside the profile of the lift, making the operator susceptible to a collision. The control arm of pallet trucks pivots from the center of the lift, allowing the lift to be controlled from multiple positions. Accidents occur when the operator is pinned between the control arm and a stationary object.
Lift Mechanism Accidents
Some of the most serious accidents often involve the lifting mechanism of the lift. The magnitude of the forces involved in the lift mechanisms of forklifts and pallet stackers can easily cause amputation or death. The mast creates pinch point hazards anywhere part of the frame can contact the ground or an object. People have been killed getting caught between the operator protection cage and the lift mast.
Roll-Over Accidents
Roll-over accidents occur when a lift is in an unbalanced or unstable state and is affected by an additional force, whether due to an impact, a shifting of a load, or the raising of the lift mast. Overturns often occur when people are working from a platform or bucket attached to the forks of a lift.
Accident Reconstruction
Safety Engineering Resources has worked on many forklift product litigation cases. Dimensional information is used to make a two-dimensional scale model of the facility and lift. Once this accurate, scaled-down representation of the accident scene is made, the objects involved in the accident can be manipulated until the reconstruction has been generated to the analyst's satisfaction.
Design Hazards of Forklifts
Guarding of Inherent Hazards
Any hazard that can be eliminated through design must be removed. Hazards that cannot be removed through design (inherent hazards) must be guarded to protect the product user and those around him or her. Hazards that cannot be neutralized with fixed guards must be brought to the attention of product users with warnings. (See Safety Engineering Resources' Warnings Manual) Engineers who guard inherent hazards with warnings without investigating guarding options are not following basic engineering design.
Operator enclosure
Engineering design principle dictates that the operator's workspace must be protected from intrusions from stationary objects and falling objects. Guarding the operator from collisions with stationary objects involves incorporating an operator enclosure into the lift design with a restraint system. An operator enclosure is a protective barrier of some sort that separates the lift operator from the hazard of foreign objects entering the workspace.
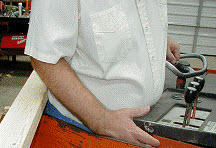
Incomplete guarding of the operator workspace can result in collision accidents
In many industrial lift-truck accidents where the operator is injured, incomplete enclosures are often found to be at blame.
Optical Sensors, Collision Detection, Bumpers and Personnel Protection Devices
Collision detection is an excellent method of protecting a lift operator from the hazards of collisions. Lifts can be fitted with sensor-equipped safety bumpers that absorb energy in the event of an impact as well as trigger an emergency stop system. These systems generally use limit switches and are relatively economical and are being used on automated guided vehicles. Other collision detection systems use optic sensors or laser scanners. These systems can be designed to prevent pedestrian-lift accidents as well.
Control Arms of Walkie Stackers
Many of these stackers use a long control arm that controls the speed of the lift. This control arm presents an impaling and crushing hazard. ANSI standards call for a safety reversing button on the end of such control arms. This safety reversing button is designed to reverse the direction of travel of the lift in the event of a collision.
Mast
The mast of a forklift is the vertical structure located at the front of a lift that raises and lowers the forks of the lift. The mast has the greatest hazard potential of any part of lift design. The mast of a lift produces a pinch point at any place where an object or body part can be caught between mechanical moving parts. The operator cab enclosure should be designed to minimize crushing and pinch point injuries between the mast and the operator enclosure. Any pinch points found in the mast of a lift should be guarded using guards.
Field of view
A forklift operator's field of view is normally wide due to the lack of any side protection on most lift operator compartments. Problems arise with visibility because of the mast - the mast creates blind spots where pedestrians could be located. Visibility is further hindered when a forklift is carrying a load.
Warning Signals and Lighting
Warning signals are advised on all lifts. Warning signals offer protection against pedestrian collisions because the signals, whether they are flashing lights or beeping sounds, alert nearby personnel of the approaching lift. Forklifts should be equipped with head lights for low-light conditions. Visibility is extremely important to safety of a moving vehicle. Reversing audible warnings are common in forklift design to prevent back-over accidents and collisions.
Environmental Factors
There are factors that affect forklift safety that are not directly related to the design of the forklift. Attorneys with clients involved in a forklift accident should be aware of the contributing effects of certain environmental factors. An investigation of the environmental factors involved in a lift accident may reveal negligence on the part of the employer.
Speed Limits
Regulating speed limits of forklifts and other vehicles can have a huge impact on the overall safety of a facility. Without a manufacturer-supplied speed control device, companies are left with the burden of setting speed limits and convincing lift operators to follow them.
Traffic Signs
Traffic signs should be used as warnings for lift operators. Signs can be developed that warn operators of upcoming hazards such as intersections, pedestrian crossings, blind corners, etc.
Factory Lay-out
The lay-out of a factory is essential to safe forklift operation. Paths and roadways specific to lifts as well as paths for pedestrians only must be laid out so that unnecessary hazards are avoided. Forklift and pedestrian pathways need to be marked clearly with high visibility paint or tape. A "dead-zone" area off-limits to pedestrians and lifts should also be designated that can act as a buffer zone. Obstructions of the field of view must be avoided.
The lift pathways must be visible under all possible lighting conditions, including emergency lighting.
Lighting
Factory lighting can have a huge impact on visibility. An insufficiently lighted area will be difficult to locate hazards in. Human factors such as the degenerative effects of aging on vision must be considered also.
When a worker cannot discriminate between objects in low light, the worker becomes more susceptible to glaring. A pedestrian may not be seen in time for a lift operator to react in low light conditions.
More Information
For more information on forklift design, safety, and product litigation issues, consider purchasing the Forklift Manual. This provides an in-depth analysis of the topics covered in this Clues and is a must-have for any attorney with a forklift product litigation case.